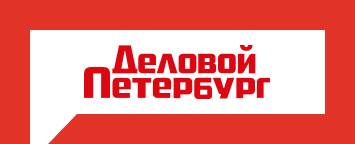
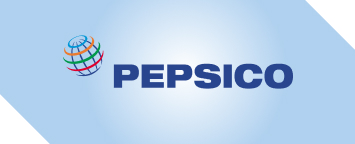
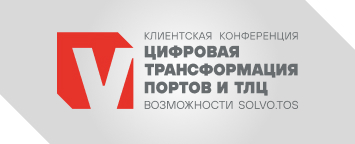
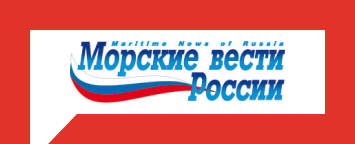
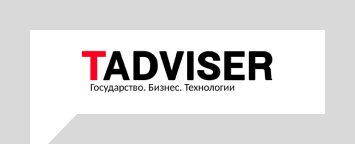
Ваш город Санкт-Петербург?
Вопрос оптимизации затрат на складскую логистику, в том числе организацию более эффективного оперативного управления зоной отбора, остается одним из самых актуальных для складских логистов и начальников складов.
Как известно, необходимость формирования запасов в системах движения товаров или материалов от поставщика к потребителю, связана с решением двух важных задач в масштабах всего бизнеса:
1. Демпфирование колебаний входящих и исходящих объемов потоков товаров;
2. Синхронизация изначально разных скоростей этих же потоков.
Для решения этих задач необходимо:
• Создавать запас и, как следствие, вести непрерывную работу для минимизации его себестоимости, то есть попытаться снизить недополученную прибыль из-за «замораживания» оборотного капитала в запасах склада;
• Нести расходы на организацию хранения и обработку запасов, это расходы на организацию склада и внутрискладскую логистику, то есть затраты, которые непосредственно увеличивают себестоимость готовой продукции.
Методикам эффективного управления запасами посвящены множество книг и статей в интернете.
Мы лишь предположим, что все эти методики в конечном итоге сводятся к попыткам прогнозирования формирования некоторого объема запаса на определенный предстоящий период времени, называемый «глубина прогноза спроса» или «срок реализации запаса», и поддержания этого объема посредством контроля и своевременного пополнения его остатка.
Обычно выбор методики и оперативное решение задач эффективного управления запасами склада на ее основе возлагается не на WMS, а на узкий круг специально обученных людей, а также систем, входящих в состав решений Supply Chain Management. Однако, внедрение SCM-решений в России – это все еще удел крупных корпораций, так как стоимость таких решений пока запредельно высока. Тем не менее проблема прогнозирования запасов остается актуальной почти для любых высокооборачиваемых складов и складов с большим количеством SKU, поэтому некоторые вендоры предлагают этот функционал в виде оптимизационных модулей своих WMS-систем под общепринятым названием slotting optimization.
Суть работы такого модуля сводится к автоматическому подбору оптимального места хранения для каждой единицы товара на складе в определенный момент времени в зависимости от изменений результатов ABC/XYZ-анализа, то есть текущего спроса и уходимости тех или иных позиций и других факторов. При этом данный функционал часто помогает менеджеру склада смоделировать ту или иную ситуацию и оценить эффект от того или иного действия.
Частным случаем задачи эффективного управления запасами склада является управление запасами зоны подпитки, или «каналами отбора».
«Каналы отбора» – это ячейка или группа ячеек, зарезервированная системой под пополнение зоны отбора под конкретный заказ. Система Solvo.WMS автоматически по правилам и стратегиям, настраиваемым пользователями, может формировать задания операторам на перемещение в эту зону необходимого в будущем товара из основной зоны хранения для обеспечения оптимального процесса пополнения зоны отбора.
Задача зоны отбора, в свою очередь, консолидировать достаточное количество номенклатуры, необходимой для непрерывного процесса отбора и комплектации заказов клиентов на ограниченной полезной складской площади при минимальном количестве операций пополнения.
Особенностью процесса является то, что одно и то же наименование может иметь несколько каналов отбора в зависимости от типа груза/контейнера. Это может быть паллета, короб, единичная упаковка.
То есть, если контролируемой единицей управления запасами всего склада является сток артикула, то единицей управления запасами зоны отбора является «канал отбора» – ячейки или области ячеек для оперативной подпитки зоны отбора.
В Solvo.WMS решение о пополнении канала отбора принимается автоматически при достижении остатком порогового значения.
Объем пополнения принимается равным разности максимального товарного запаса и его текущего остатка.
В интерфейсе Solvo.WMS это представляет собой так называемые «счетчики каналов», где есть три пороговых значения, при достижении которых система может автоматически запустить задание на пополнение канала в зависимости от принятой администратором WMS стратегии:
• Max (максимальный объем товара в канале) – количество товаров в канале меньше или равно физически доступной вместимости зоны отбора;
• Optimal (точка заказа/пополнения канала отбора) – оптимальное количество товара в канале – это переходящий неснижаемый остаток зоны отбора;
• Min (фактически это страховой запас канала отбора) – минимально возможное количество товаров в канале для пополнения зоны отбора или страховой запас зоны отбора.
Пользователю WMS предоставлена возможность самостоятельного выбора методики расчета значений этих параметров и их своевременного обновления.
Последствия выбора неоптимальных значений параметров трудно переоценить, ведь ошибки влекут за собой целый ряд негативных последствий, причем как для самой зоны отбора, так и для склада в целом. Например, если установленные значения выше оптимальных, то результатом будет нецелесообразное использование складской площади: зона отбора будет занимать больше места, чем могла бы, следовательно, скорее всего, увеличится протяженность маршрутов и время сбора заказов сборщиками. Все это приводит к хроническому дефициту площади и затоваренности зоны отбора, а значит – к дополнительным затратам на организацию вытеснения неиспользуемого запаса зоны отбора обратно в зону хранения.
Если установленные значения меньше необходимых оптимальных, результатом будет увеличение количества операций пополнения и, как следствие, неоправданные затраты всех видов складских ресурсов (времени, техники, людей) для их выполнения, дефицит номенклатуры в зоне отбора и вынужденный простой процесса отбора заказов в ожидании пополнения зоны подпитки. Самым худшим сценарием развития событий в данном случае может стать срыв суточного графика отгрузок заказов клиентов, особенно в высокий сезон.
Таким образом эти параметры оказывают существенное влияние и на стоимость запасов склада, и на себестоимость готовой продукции, и на коэффициенты удовлетворения клиентского спроса и уровня сервиса. Если на складе выявились некоторые из перечисленных негативных признаков, то, вероятно, имеет смысл поискать узкие места в управлении запасами зоны подпитки. Для предотвращения подобных проблем в системе Solvo.WMS есть механизм тонкой настройки счетчиков каналов отбора, который позволяет эффективно управлять зоной отбора, подбирая значения для максимального объема товара в канале, точки заказа/пополнения канала, страхового запаса зоны отбора. Функционал дает возможность оперативно учитывать изменения текущих параметров расхода номенклатуры в каждом канале отбора в режиме реального времени.
На практике регулярно рассчитывать и поддерживать значения указанных параметров каналов отбора актуальными и оптимальными не так просто. Специалисты в области прогноза и планирования запасов, если таковые имеются в штате, обычно заняты этим вопросом в масштабах склада, и у них нет ресурса проводить такой расчет для каждой зоны. Выполнять же такую работу самостоятельно силами сотрудников склада – задача не из легких, не говоря уже о трудоемкости процесса: вручную оперативно и систематически посчитать и, следом, изменить параметры каналов отбора – достаточно сложно.
Однако решение все же существует.
Все методики расчета начальных параметров системы управления запасами при непрерывном контроле фактического остатка запаса сводятся к попытке прогноза объема расхода номенклатуры (это и есть максимальное значение канала отбора) на некий предстоящий период времени, именуемого «срок реализации расчетного оптимального запаса».
То есть все построено на математическом анализе числовой последовательности значений расхода и остатка номенклатуры в каждом канале отбора, сгруппированных, к примеру, посуточно. Тем не менее, специалисты компании «СОЛВО» помогут настроить и автоматизировать в Solvo.WMS любой удобный алгоритм расчета параметров системы управления с двумя уровнями при непрерывном контроле фактического остатка запаса и нулевом плече доставки.
Один из вариантов алгоритмов был реализован в зоне отбора единичными упаковками на складе одного из клиентов «СОЛВО» – фармацевтического дистрибьютора в Санкт-Петербурге – и показал хорошие результаты.Для его выполнения стояла задача определения глубины прогноза – так называемого срока реализации планируемого запаса – для расчета предстоящего расхода, под который необходимо формировать запас номенклатуры в канале отбора.
Номенклатура с высокой скоростью движения и объемом расхода в канале отбора, скорее всего, будет требовать разумного ограничения этого объема и, как следствие, регулярного его пополнения с какой-то приемлемой частотой и объемом.
С другой стороны, каналы отбора с позициями совсем малого объема и скорости реализации предсказуемо потребуют не более одной единицы транспортной тары/упаковки в канале отбора, которой хватит на значительный срок реализации.
Миграция номенклатуры между этими крайними состояниями в любом направлении, например, вследствие сезонности спроса, требует своевременного изменения оптимального объема канала отбора.
Задача определения необходимой и достаточной глубины прогноза оптимального объема для канала отбора или срока реализации сводится к необходимости анализа характера расхода номенклатуры в каждом канале отбора и ее группировки по неким общим признакам, и, далее, присвоения каждой полученной группе номенклатуры «своего» срока реализации в качестве постоянной.
Таким образом, попадание номенклатуры в группу на основе анализа характера параметров ее расхода позволит нам определить глубину прогнозируемого периода времени, под который на следующем этапе предстоит рассчитать параметры управления каналом ее отбора.
1. ABC-анализ – анализ объема;
2. DIP-анализ – Deep Packet Inspection (сокр. DPI) – анализ товарного ассортимента по частоте обращений/взятия;
3. FMR (англ. Fastest Medium Rare – быстро, средне, медленно). Иногда также применяются термины:
• FSN (англ. Fast moving, Slow moving, Non Moving) и FNS (англ. Fast Moving, Normal Moving, Slow Moving);
ABC-анализ по количеству отборов – это и есть группировка номенклатуры по частоте обращения к ней – DIP.
В XYZ-анализе в данном случае нет необходимости, так как чаще всего невозможно воспользоваться результатами его приме- нения для зоны отбора, потому что размер коэффициента вариации суточного объема расхода у большинства позиций номенклатуры не позволит сгруппировать ее по этому принципу, а предварительная подготовка начальных данных для такого анализа, например, их очистка от влияния сезонности, потребует уникального подхода в каждом отдельном случае.
Теперь обратимся к примеру выше. Какой же метод расчета следует применить? С учетом того, что каждый тип аналитики и группировки увеличивает количество групп в геометрической прогрессии (3, 9, 27), то можно рекомендовать ограничиться максимум двумя наиболее подходящими методами, например, из представленных на картинке слева:
- по количеству отборов;
- по любому из трех оставшихся на усмотрение пользователя в зависимости от характеристик номенклатуры.
В результате вы получаете группировку номенклатуры в каналах отбора одновременно по двум выбранным параметрам расхода. WMS-система может выдать табличный отчет, содержащий минимум девять групп номенклатуры.
Для каждой из полученных групп на основе методики расчета параметров системы управления запасами зоны отбора и текущей статистики расхода/остатка пользователь может легко подобрать, определить и присвоить в качестве постоянного параметра свой оптимальный для этой группы номенклатуры срок реализации планируемого запаса.
Антон Артев, бизнес-аналитик «СОЛВО»
Даниил Першин, руководитель отдела маркетинга «СОЛВО»