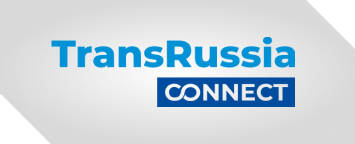
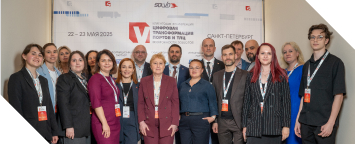
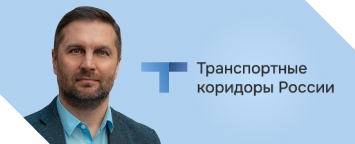
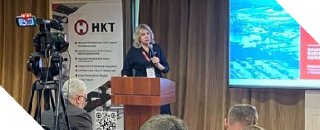
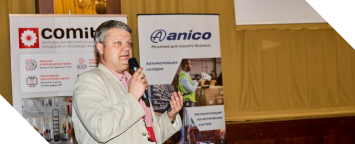
Ваш город Санкт-Петербург?
Такой вопрос мы получили от подписчиков наших новостей и решили раскрыть эту тему подробнее.
Под контролем обработки заказов на складе мы можем понимать две функции:
1. Контроль исполнения обработки заказов на складе менеджером (администрирование).
2. Контроль качества сборки заказов
На складах продуктов питания к стандартным алгоритмам системы, организующим контроль по этим двум направлениям, также добавляется учет сроков годности продуктов и сборка заказов с учетом температурных режимов, весовых характеристик товара и совместимости грузов.
В данном случае менеджеру сборки заказов должна быть доступна вся необходимая информация для того, чтобы понимать, насколько выполнена в настоящий момент сборка того или иного заказа (или заказов) и нужны ли с его стороны какие-либо корректирующие воздействия.
Для этого в системе Solvo.WMS есть все необходимые инструменты, которые помогают контролировать как процесс сборки одного заказа, так и целого рейса (маршрута), волны заказов.
Если речь идет об одном заказе, то система Solvo.WMS автоматически формирует список всех необходимых работ с распределением задач для сотрудников. Менеджеру остается только просмотреть этот список и запустить процесс сборки.
Решение проблем при сборке. При наличии каких-либо проблем с данным заказом, менеджер видит специальный признак наличия проблемы в заказе и далее можете перейти в листы отбора и посмотреть более детальную информацию в проблемном листе: какую часть груза не удалось спланировать или собрать, где возникли трудности на этапе планирования заказа (например, если какого количества товара не хватает, груз не подходит под нужные параметры и так далее), какое количество товара не дособрал оператор и почему? В случае необходимости можно дать системе команду автоматически перепланировать проблемные строчки. А если вопрос требует участия менеджера, то он сам вносит свои коррективы.Расстановка приоритетов. В случае с несколькими заказами, при необходимости, менеджер склада может повышать приоритет каких-то из них. Например, если поступил срочный незапланированный ранее заказ или изменилось время выполнения одного из запланированных, он может вручную поднять приоритет заказа, и система назначит сотрудникам склада приоритетные работы по сборке. Также менеджер может выбрать для выполнения приоритетной работы конкретного исполнителя (или группу исполнителей). Например, самого опытного, ответственного или оперативного по его мнению специалиста. И, пока исполнитель не выполнит поставленные задачи, другие не будут ему назначаться.
Также Solvo.WMS помогает менеджеру контролировать более сложные варианты сборки, когда речь идет о группе заказов. Например, когда собирается рейс или волна. Он видит общую картину по сборке определенной группы заказов, имеет возможность перейти и посмотреть детально информацию по конкретному выбранному заказу и, при необходимости, принять какие-либо управленческие решения.
Сборка рейса. Когда нужно собрать группу заказов в рейс - на определенный автомобиль - система Solvo.WMS позволяет в режиме одного окна оперировать заказами по всему маршруту, если данные об этом рейсе внесены в систему еще до старта сборки. У менеджера в системе появится отдельное окно с названием рейса и группой заказов по нему. Как и в случае с одним заказом, он будет получать уведомления по всем заказам данной группы, видеть проблемные моменты, решать их, обращаясь при необходимости к каждому отдельному заказу внутри группы. Обычно рейс формируется в системе управления транспортом (TMS) и далее по межсистемному интерфейсу передается в Solvo.WMS. Идеальным является вариант, когда рейс сформирован еще до момента начала сборки заказов, тогда в процессе сборки можно оперировать рейсом, а не отдельными заказами.
Сборка волны. Аналогичный вариант с волной - объединением заказов, которые собираются к определенному времени. К примеру, это могут быть 5, 10, 15, 20 рейсов, которые запланированы на определенное время. Рейсы, внутри которых уже сгруппированы заказы, в свою очередь, группируются в волны к определенному времени. Внутри системы, в режиме одного окна, менеджеру доступны экраны с информацией о каждой волне, о каждом рейсе, о каждом отдельном заказе внутри этих групп. Он видит экраны текущих работ, использует удобные переходы внутри каждой волны - все экраны связаны между собой. Если нужно посмотреть работы по заказу внутри определенной волны, система отфильтрует и покажет только работы, связанные с данной группой.
Из экрана волны можно войти в экран заказа, а оттуда – в экран работ, чтобы подробно посмотреть, какой сотрудник и какую работу выполняет, какова стадия реализации сборки каждого заказа. Так, менеджер видит всю картинку внутри склада а, при необходимости, может выбрать определенную ее часть, «приблизить», «рассмотреть» подробно и детально вплоть до текущего отбора – в системе есть возможность видеть текущий экран конкретного оператора ТСД и, в случае необходимости, подключиться и скорректировать его действия.
Система Solvo.WMS в автоматизированном режиме помогает менеджеру склада следить и за качеством исполняемых работ, назначая задания сотрудникам и технике. При входе в систему каждый оператор указывает, с какой единицей техники он работает. Система, в свою очередь, учитывает при назначении работ характеристики данного вида техники, возможности и ограничения самого оператора. Например, сколько паллет или коробок способна перевезти техника, который управляет данный специалист, какова ее грузоподъемность, какова доступность для нее той или иной зоны склада, есть ли у оператора возможности работать на верхних и нижних ярусах, выполнять те или иные операции.
Когда человек входит в систему, идентифицируя себя и указывая технику, с которой он будет работать, система учитывает пересечения всех возможностей и ограничений, и выдает наиболее приоритетную из доступных на данный момент работ. Причем, приоритезация – процесс динамический. Он учитывает очень много различных факторов. Не просто один приоритет, а много видов приоритетов. Например, по типу работы, по приоритету прикрепленного к заказу документа, по расстоянию от человека до места выполнения задачи, по времени создания работы и так далее. И все эти вычислительные процессы длятся какие-то секунды.
Система может назначать сотруднику работы как по одному, так и сразу по волне заказов, используя технологию мультипикинга (процесс одновременного отбора нескольких заказов), в зависимости от поставленных задач и приоритетов. Менеджер, в свою очередь, может ограничить в настройках системы объем и состав собираемой продукции в рамках листа или по объему, исходя из потребностей склада.
Также система поддерживают технологию put-to-store, которая позволяет сделать консолидированный отбор общего количества товара под требования всех заказов волны, а потом система формирует задание на развоз по специальному маршруту для сортировки данного товара в соответствии с требованиями конкретного заказа.
Сроки годности. Система учитывает этот параметр при назначении заданий по сборке заказов. Например, есть клиенты, по контракту с которыми срок годности продукции не должен истечь более, чем на 90% на дату отгрузки, а кому-то приемлемо, если эта сумма будет составлять 60%. Эти параметры вводятся в систему, и она учитывает их при назначении задач сотрудникам и техники. К примеру, в заказе на сборку будет просто отмечено, что нужно отгрузить 10 коробок со сметаной, но, в зависимости от контракта с клиентом, система назначит на погрузку совершенно разные коробки с разными партиями продукции, в соответствии со сроками хранения.
Сборка с учетом температурного режима. В данном случае система будет учитывать, собирается ли в один рейс одновременно продукция из холодильной и сухой зон склада и распределит выгрузку этой продукции так, чтобы соблюсти требования к хранению и дальнейшей транспортировке продукции в соответствии с температурным режимом.
Сборка расфасованного весового товара. Такие продукты как мясо, рыба, овощи, фрукты нередко отгружаются клиенту по указанному весу. В таком случае система Solvo.WMS может быть интегрирована с весовым оборудованием склада, либо учитывать уже расфасованную продукцию с конкретным весом. Можно задать настройки, при которых Solvo.WMS подберет ровный вес такой продукции, указанный в заказе клиента.
После отбора продукции зачастую организуется процесс контроля качества, в рамках которого решаются две задачи:
Контроль качества работы отборщика
Переупаковка продукции и подготовка ее к отгрузке исходя из требований клиента
Для этого в системе Solvo.WMS существует операция «Упаковка», которая поддерживает режимы упаковки по грузовым местам (в соответствии с уникальным кодом паллет или коробок с грузом), по нужному количеству товара (когда, к примеру, берется часть коробок из одной паллеты). При упаковывании можно вести как поштучный учет товара (когда через сканер проводится каждая единица продукции, как на кассе в супермаркете), так и принимая сразу весь контейнер без детальной проверки того, что внутри (например, в случаях двухстадийной упаковки, когда в мезонине ранее уже был осуществлен предварительный учет штучной продукции и ее упаковка, а далее товар упаковывается в соответствии с требованиями клиента - по высоте и размеру паллеты и так далее).
Каждая грузовая единица, прошедшая данную процедуру в системе, получает соответствующий статус «Упакован», и менеджер отгрузки в режиме реального времени видит какая из них уже упакована, а какая еще нет.
Таким образом на продуктовом складе упрощается процесс администрирования управления и повышается качество сборки. Это ускоряет время сборки, снижает риски путаницы и порчи грузов, помогает расставлять приоритеты работ и правильно назначать задачи технике и персоналу.